دسترسی آسان به مطالب
شاخص جریان مذاب
شاخص جریان مذاب : سرعت جریان مذاب (MFR) ساده ترین روش استاندارد برای تعیین و مقایسه رفتار مذاب گونه های مختلف پلیمرهای گرمانرم است. هرچه MFR یک نمونه مذاب پلیمری بیشتر باشد بدان معناست که ویسکوزیته آن کمتر است و هر چه ویسکوزیته کمتر باشد میتوان نتیجه گرفت که وزن مولکولی آن نمونه پایین تر است لذا میتوان گفت که MFR ساده ترین روش استاندارد برای مقایسه نسبی وزن مولکولی گریدهای مختلف پلی اتیلن است. شاخص جریان مذاب بصورت مقدار ماده مذابی تعریف میشود که در مدت 10 دقیقه تحت بار معین و در دمای مشخص از دای با ابعاد مشخص خارج میشود. این مقدار با واحد g/10min بیان میشود و مقدار آن برای محصولات تولیدی با مواد HDPE 3840 به روش روتاری مولدینگ (5/4-8/3) میباشد.
تشخیص سوختن
دو مورد سوختن و پخت ناقص از ظاهر قطعه قابل تشخیص میباشد. به این صورت که در صورت سوختن، قطعه براق شده و رنگ آن متمایل به قهوه ای میشود. در صورت پخت ناقص روی سطح قطعات جوش های کوچک تشکیل میشود.
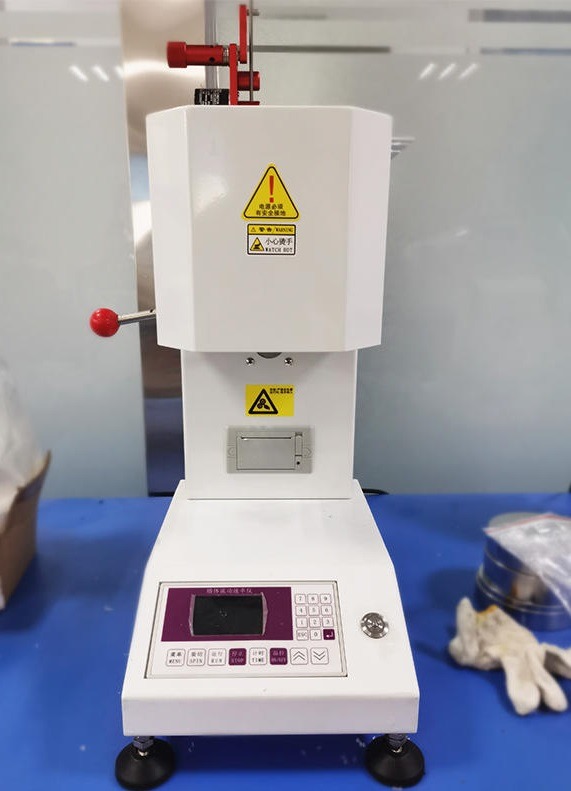
اهمیت شاخص جریان مذاب
- انتخاب فرایند مناسب: جریان مذاب به مهندسان پلیمر کمک میکند تا فرایند مناسب برای تولید یک محصول پلیمری را انتخاب کنند. برای مثال، پلیمرهایی با جریان مذاب بالا برای فرایندهایی مانند اکستروژن مناسبتر هستند، در حالی که پلیمرهایی با جریان مذاب پایین برای قالبگیری تزریقی مناسبترند.
- کنترل کیفیت: جریان مذاب یک ابزار مهم برای کنترل کیفیت محصولات پلیمری است. تغییرات در جریان مذاب میتواند نشاندهنده تغییرات در خواص پلیمر یا فرایند تولید باشد.
- طراحی فرمولاسیون: دانستن جریان مذاب به طراحان فرمولاسیون کمک میکند تا فرمولاسیونهای پلیمری با خواص مطلوب را ایجاد کنند.
عوامل موثر بر شاخص جریان مذاب
- وزن مولکولی پلیمر: هرچه وزن مولکولی پلیمر کمتر باشد، زنجیرههای پلیمری کوتاهتر بوده و در نتیجه پلیمر روانتر خواهد بود. بنابراین، جریان مذاب با کاهش وزن مولکولی افزایش مییابد.
- دمای ذوب: با افزایش دمای ذوب، ویسکوزیته پلیمر کاهش یافته و جریان مذاب افزایش مییابد.
- فشار اعمال شده: افزایش فشار باعث افزایش سرعت جریان مذاب و در نتیجه افزایش جریان مذاب میشود.
- ابعاد روزنه: با افزایش قطر روزنه، مقدار بیشتری از پلیمر میتواند در مدت زمان مشخص خارج شود و در نتیجه جریان مذاب افزایش مییابد.
واحد جریان مذاب
واحد معمول MFR گرم بر دقیقه (g/min) است.
روش اندازهگیری
جریان مذاب با استفاده از دستگاهی به نام دستگاه اندازهگیری شاخص جریان مذاب اندازهگیری میشود. در این دستگاه، نمونه پلیمری در یک سیلندر گرم شده قرار میگیرد و تحت فشار مشخصی از یک روزنه با ابعاد مشخص خارج میشود. مقدار پلیمری که در مدت زمان مشخص خارج میشود، وزن شده و جریان مذاب محاسبه میشود.
کاربردهای جریان مذاب
- صنعت پلاستیک: برای انتخاب نوع پلیمر مناسب برای تولید محصولات مختلف مانند لوله، ورق، فیلم و …
- لاستیک: برای کنترل کیفیت لاستیکهای مختلف
- نساجی: برای تولید الیاف مصنوعی
مزایای شاخص جریان مذاب
شاخص جریان مذاب به عنوان یک پارامتر کلیدی در صنعت پلیمر، مزایای متعددی را برای تولیدکنندگان و مصرفکنندگان محصولات پلیمری به ارمغان میآورد. در زیر به برخی از مهمترین مزایای MFR اشاره میشود:
- کنترل کیفیت
- بهینهسازی فرایند
- انتخاب مواد اولیه مناسب
- توسعه محصولات جدید
- تضمین کیفیت محصول
- طول عمر بیشتر محصول
- تنوع محصولات
- کاهش ضایعات
- افزایش بهرهوری
- توسعه پایدار
روشهای اندازهگیری شاخص جریان مذاب
شاخص جریان مذاب یکی از مهمترین پارامترهای مشخصکننده خواص جریانپذیری پلیمرهای گرمانرم است. برای اندازهگیری دقیق این شاخص، از دستگاههای مخصوصی به نام دستگاه اندازهگیری شاخص جریان مذاب استفاده میشود.
- گرم کردن نمونه: نمونه پلیمری در یک سیلندر گرم شده قرار میگیرد تا به دمای ذوب برسد.
- اعمال فشار: یک پیستون یا وزنه به نمونه فشار وارد میکند تا مذاب پلیمر از یک روزنه با قطر مشخص خارج شود.
- تعیین مقدار مذاب خروجی: مقدار پلیمری که در مدت زمان مشخص (معمولاً 10 دقیقه) از روزنه خارج میشود، اندازهگیری شده و بر حسب گرم بر دقیقه (g/min) بیان میشود.
دستگاه اندازهگیری MFR
این دستگاهها به طور کلی شامل اجزای زیر هستند:
- سیلندر گرم شده: برای ذوب کردن نمونه پلیمر
- پیستون یا وزنه: برای اعمال فشار به نمونه
- روزنه با قطر مشخص: برای کنترل سرعت جریان مذاب
- تایمر: برای اندازهگیری زمان جریان
- جمعکننده مذاب: برای جمعآوری و وزن کردن مذاب خروجی
عوامل موثر بر دقت اندازهگیری
- دقت دما: دمای سیلندر باید با دقت کنترل شود، زیرا تغییرات دما به طور مستقیم بر ویسکوزیته مذاب و در نتیجه MFR تأثیر میگذارد.
- دقت فشار: فشار اعمال شده به نمونه نیز باید با دقت کنترل شود.
- قطر روزنه: قطر روزنه باید دقیقاً مطابق با استاندارد باشد.
- وزن نمونه: وزن اولیه نمونه باید دقیقاً اندازهگیری شود.
- زمان اندازهگیری: زمان اندازهگیری باید با دقت کنترل شود.
ارتباط جریان مذاب با فرآیند شکلدهی
- سیالیت مذاب: جریان مذاب بالا نشاندهنده سیالیت بیشتر مذاب است. این بدان معنی است که پلیمر با MFR بالا راحتتر در قالب جریان مییابد و پر شدن قالب را تسهیل میکند.
- پر شدن قالب: برای فرایندهایی مانند تزریق، اکستروژن و قالبگیری دمشی، سیالیت مناسب مذاب برای پر شدن کامل قالب و تولید قطعات با هندسه پیچیده ضروری است.
- فشار تزریق: پلیمرهایی با جریان مذاب پایین به فشار تزریق بالاتری نیاز دارند تا بتوانند قالب را پر کنند. این امر میتواند منجر به افزایش تنش در قالب و کاهش عمر قالب شود.
- زمان چرخه: پلیمرهایی با جریان مذاب بالا زمان چرخه تولید را کاهش میدهند، زیرا سریعتر قالب را پر میکنند.
- کیفیت سطح: سیالیت بیش از حد مذاب ممکن است منجر به ایجاد خطوط جریان و سطح ناهموار در قطعه شود.